Performances
Inverter Efficiency Improvement
The efficiency improvement in the inverter comes from the fact that the voltage increase generated by the Capacitive Boost Processor occurs downstream of the inverter, unlike a conventional topology in which a DC/DC converter steps up the voltage upstream of the inverter. When the inverter input voltage is reduced, the switching losses in the transistors decrease due to the lower voltage levels at which they operate. The switching losses are mainly caused by the voltage and current overlapping during the transition between the on and off states of the transistor. A lower input voltage results in a reduced voltage difference across the device during switching events, which reduces the energy dissipated during these transitions. As a result, the overall switching loss decreases, leading to improved efficiency and lower heat generation in the inverter system.
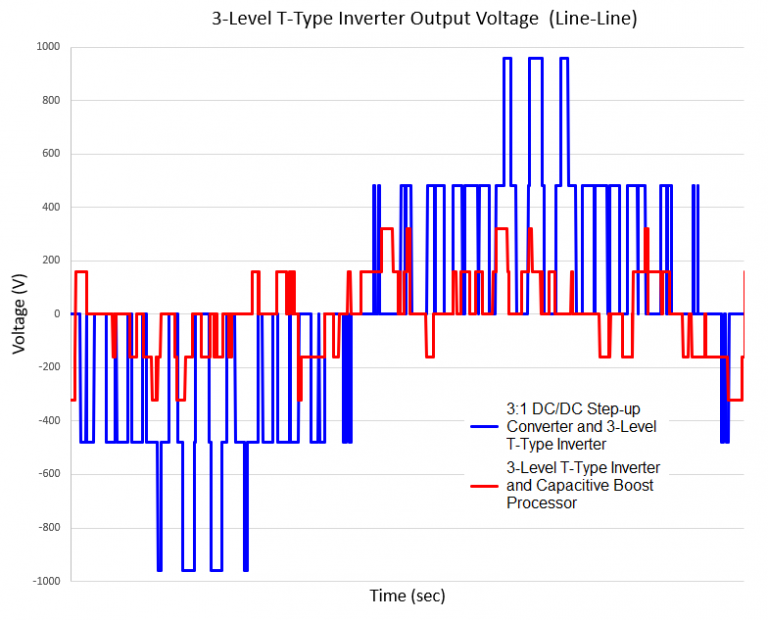
Zero Current Switching
The Capacitive Boost Processor operates in zero or near-zero current switching. Zero-current switching (ZCS) offers significant advantages in reducing switching losses in transistors. In zero-current switching, transistors turn on or off when the current through them is zero, thereby minimizing the overlap between the voltage and current waveforms during switching transitions. This reduces the energy dissipated as heat during these transitions, since little or no current flows when the transistor switches, avoiding high power losses. As a result, zero-current switching improves overall efficiency, reduces thermal stress on components, and increases transistor life, making it particularly advantageous in power electronics applications where efficiency is critical.
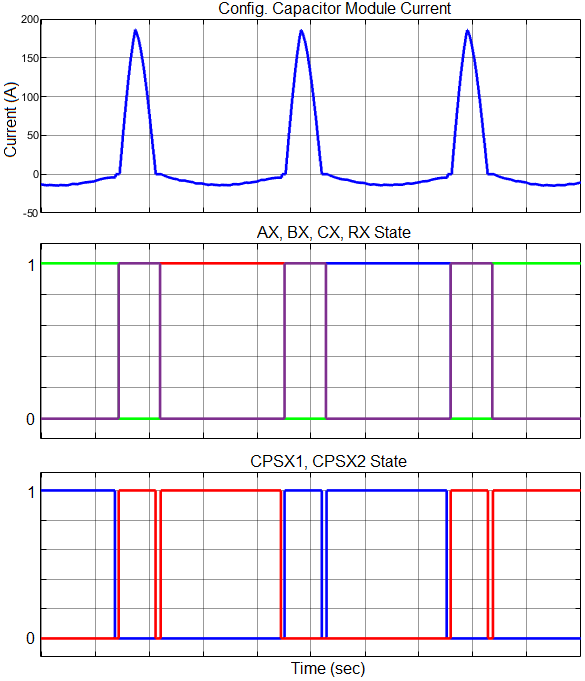
Motor Efficiency Improvement
When the total harmonic distortion (THD) of the phase current in a permanent magnet synchronous motor (PMSM) is reduced, the iron losses in the motor also decrease. Iron losses, which include hysteresis and Eddy current losses, are influenced by the shape of the current waveform. High THD results in a non-sinusoidal current that generates fluctuating magnetic fields, causing increased iron losses in the stator core. By reducing the THD, the current waveform becomes closer to a pure sine wave, leading to a more stable magnetic field and reduced variations in the core flux. This results in lower hysteresis and Eddy current losses, which improves motor efficiency and reduces heat generation.
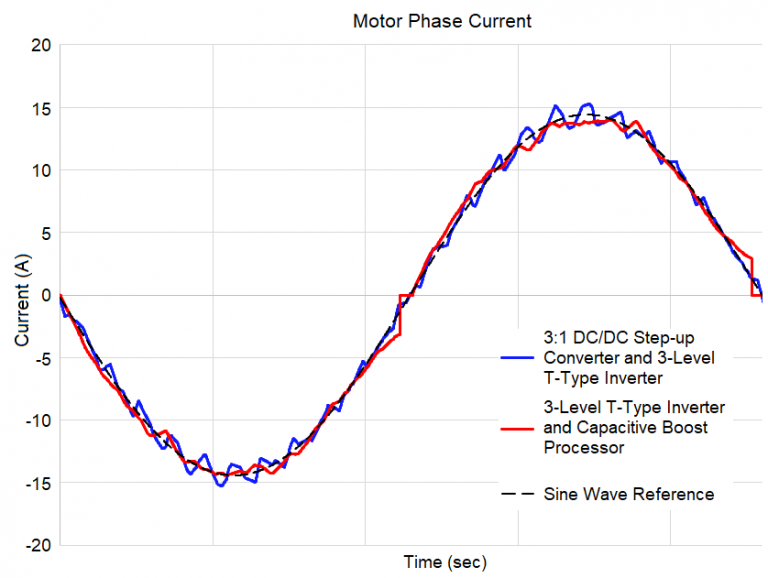
Power Density Increase
Simulation results show that the technology can increase the power density of an ABB BSM33C-6177 motor by 325% compared to its rated power at nominal voltage. The increase in power density comes from the fact that maximum torque is available up to 325% higher speed. This feature makes the technology ideal for applications where space and weight are critical, such as in electric vehicles and aerospace. This technological advancement leads to more compact and higher-performance systems with reduced use of iron, copper and permanent magnets.
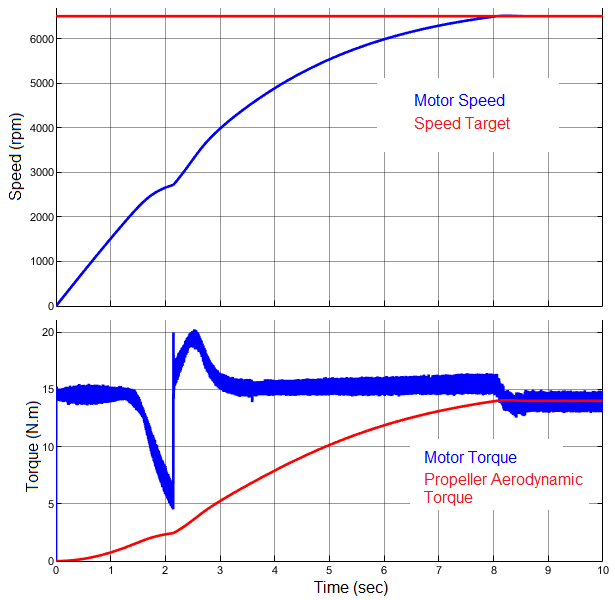